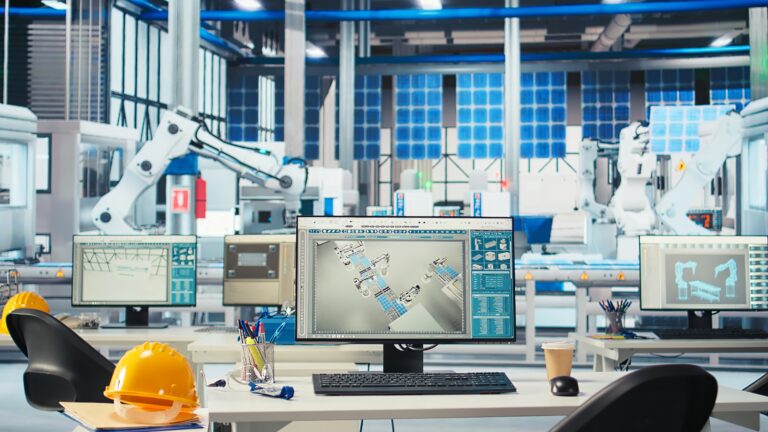
In today’s competitive manufacturing landscape, companies are under constant pressure to increase efficiency, reduce downtime, and stay ahead of technological trends. One of the most powerful ways to achieve this is through robust PLC SCADA HMI systems that offer complete control, automation, and monitoring across industrial processes.
At AIP, we specialize in offering end-to-end PLC SCADA HMI development and commissioning services, focusing on how our clients actually search for solutions like “automating manual processes,” “real-time factory monitoring,” or “PLC and HMI integration that meets global standards.” This blog walks you through the best practices from design to deployment, with insights into real-time monitoring, system integration, and achieving maximum ROI.
Key Takeaways
- PLC, SCADA, and HMI systems form the backbone of modern factory automation by ensuring seamless control, real-time visibility, and operator interaction.
2. Following best practices during design, development, and commissioning ensures higher uptime, fewer errors, and long-term reliability.
3. Integration of PLC and HMI reduces manual intervention on the factory floor and improves operational efficiency.
4. Real-time process monitoring through SCADA helps factories track performance, reduce downtime, and make smarter decisions.
5. AIP offers end-to-end automation solutions customized to each client’s needs, aligned with industry standards, and built for scalability.
Table of Contents
1.Why PLC SCADA HMI Systems Are Crucial for Modern Manufacturing
- Manpower and machines are no longer the only things found in factories. They’re evolving into intelligent systems where data, automation, and control need to work in perfect harmony. This is where PLC SCADA HMI solutions are useful.
- PLC (Programmable Logic Controller) executes control functions based on real-time sensor inputs.
- Centralized data collection and visualization are offered by SCADA (Supervisory Control and Data Acquisition).
- HMI (Human-Machine Interface) allows operators to interact with machines and receive live feedback.
- For manufacturing clients looking for greater efficiency and fewer manual interventions, implementing these systems can be a game-changer.
2. Step 1: Understanding Requirements and Scope
The first step in any PLC SCADA HMI commissioning project is understanding the client’s pain points and goals.
Example Search Queries by Clients:
- “How to automate manual valve operations in a bottling plant”
- “Need to integrate existing PLCs with modern SCADA systems”
We start with:
- A factory audit
- Reviewing existing processes and electrical layouts
- Identifying points of failure and bottlenecks
We ensure all automation aligns with production KPIs, energy usage goals, and global safety standards.
3. Step 2: PLC and HMI Integration Planning
Connecting a screen to a controller is only one aspect of PLC and HMI integration. It involves:
- Designing intuitive HMI screens based on user workflows
- Mapping PLC logic to screen functionalities
- Ensuring real-time communication with minimal latency
Client Example: An automotive Tier-1 supplier needed centralized machine controls. We developed modular PLC code and custom HMI templates aligned with VASS (Volkswagen) standards. As a result, the client experienced smoother machine setup, improved usability, and faster production readiness.
4. Step 3: Hardware & Software Design
We work with globally recognized PLC and HMI platforms, ensuring reliable and scalable automation solutions. Our engineering team designs:
- Electrical panels with safety interlocks
- PLC program logic for sequence control
- SCADA systems for remote access and analytics
We also simulate conditions using digital twins to reduce errors in real-world commissioning.
5. Step 4: Real-Time Process Monitoring Setup
Modern manufacturing relies heavily on real-time process monitoring. Clients often ask:
- “Can I track production output minute-by-minute?”
- “How do I get alerts before equipment failure?”
We deploy: To ensure system reliability and immediate insight into deployment health, real-time process monitoring must be configured.
- SCADA dashboards with drill-down analytics
- Alerts for temperature, pressure, and cycle deviations
- Data storage for batch history, quality checks, and traceability
What You Gain: These setups help manufacturers quickly identify anomalies, reduce waste, and maintain consistent quality across operations.
6. Step 5: Testing and Onsite Commissioning
Once systems are built, we conduct:
- Pre-commissioning in our in-house lab
- On-site testing with client operators
- Safety checks, I/O mapping, and emergency stop validation
We ensure complete documentation and provide client training sessions for HMI use, SCADA dashboard interpretation, and troubleshooting.
7. Step 6: Post-Commissioning Support and Optimization
Our job doesn’t end after deployment. We:
- Offer 24/7 remote support
- Regularly upgrade PLC logic to match process changes
- Optimize SCADA databases for faster query results
We also help standardize automation across multiple plants, allowing clients to scale operations globally with minimal effort.
8. Why Choose AIP for PLC SCADA HMI Solutions?
We understand what our industrial clients need because we listen first, then solve.
- Real Use Cases: We’ve improved uptime, efficiency, and safety across the automotive, pharmaceutical, and energy sectors.
- Global Compliance: Our solutions meet standards like INTEGRA, TMO, and VASS.
- Tailored Solutions: Every plant, every process is different. We adapt accordingly.
Final Thoughts
Your competitors are already embracing automation. The real question is: how fast can you adopt the right PLC SCADA HMI system before falling behind?
Whether it’s integrating legacy systems, enabling real-time process monitoring, or creating intuitive PLC and HMI integration, we’re here to partner with you at every step.
Looking to upgrade your plant automation or integrate a smarter monitoring solution? Reach out to AIP for a consultation tailored to your factory’s goals.
FAQs
Can you upgrade my existing PLC/SCADA systems?
Yes, we specialize in retrofitting old systems with minimal downtime.
Do you work with international OEM standards?
Absolutely. We work with clients adhering to VASS, TMO, and INTEGRA protocols.
What industries do you serve?
Automotive, energy, chemicals, warehousing, pharmaceuticals, and more.
How long does a commissioning project take?
Depends on the scope. Ranges from 2 weeks to 3 months.
Do you offer cloud-based SCADA solutions?
Yes. We offer on-premise, hybrid, and fully cloud-based setups.